Polymers in inkjet inks
Polymers play the most important part in inkjet inks, comparable, perhaps, only to the colorants themselves. Without polymers, colorants will not be able to bind to the media they are being printed upon, and will be washed off or rubbed off. The durability and the adhesion to the substrate are essential for the inkjet functionality. This feature is in most of the cases in a direct conflict with the inkjet reliability. The high polymeric durability on the printed substrates also causes undesirable side effects of deposits inside and outside inkjet nozzles and on the orifice plate.
One has to remember that every inkjet nozzle of water-based inkjet inks loses water at the rate of a few nanograms per second. Although it does not sound as much, the fluid chamber of an inkjet nozzle is only few picoliters/nanograms in size. As the result, in a few seconds, the concentration of the polymer at the tip of the nozzle becomes as high as 10 -30 wt%. Many polymers at this concentration form a very thick gel and the printhead becomes irreversibly clogged.
In order to prevent the nozzle from clogging, the molecular weight of the polymer needs to be kept on a lower side. Also, polymers with highly branched architecture can generate more compact polymeric coils with less overlap, and, therefore reduce the overall system viscosity.
Emulsion and dispersion polymers offer an intrinsic advantage in terms of the reliability over the linear chain polymers. As water evaporates from a polymeric dispersion, there is no coil overlap and gelation effects. The polymeric particles become jammed only at a relatively high volume fraction, ~ 0.5, whereas polymeric solutions can gel at a much lower concentration, as low as 0.01, see Figure 1.
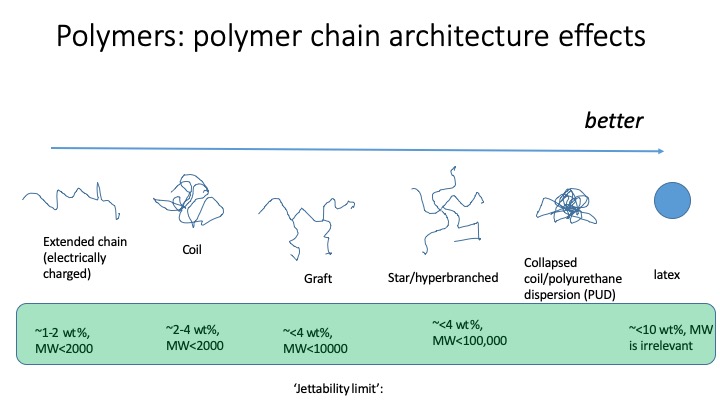
Figure 1. Polymeric chain design and inkjet reliability
Table 1. Functions of polymers in inkjet inks
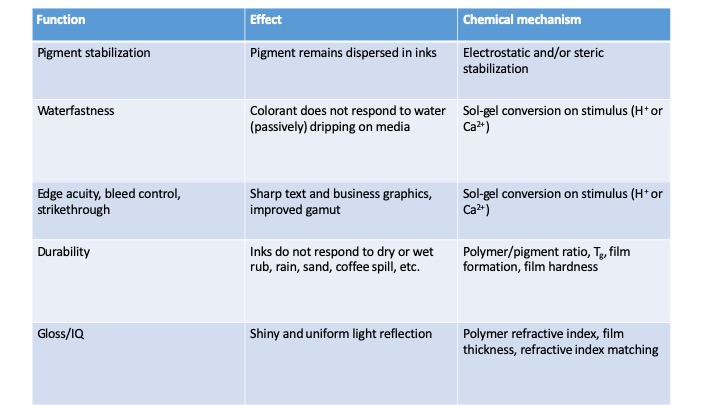
Beyond durability, polymers in inks serve many other functions. Many inkjet polymers are polyelectrolytes with solubilizing carboxylic groups. As many inkjet papers are strongly acidic, inkjet polymers in situ convert from the carboxylate to carboxylic acid form on the media. As a result, the ink becomes water insoluble and gels up, improving image quality attributes, such as the text and line edge acuity, bleed, optical density and strike-through. By contrast, as the acidity of sulfo group is much higher, sulfonated polymers do not provide such function. Other functions of polymers in inkjet inks are summarized in Table 1.